Turbo Part Variations
Over the years turbocharger components have evolved incorporating several design enhancements to improve the efficiency and overall performance of the turbocharger, in line with engine advancements. We have created a series of component fact sheets highlighting specific component variations:
Shaft & Wheel Development
Common turbo failures such as overspeeding can cause severe fatigue to the shaft and wheel. Signs of fatigue include partial loss of blades caused by the constant flexing of blades beyond the designed parameters. Fatigue is a mode of failure not the cause.
Traditionally, a shaft and wheel has an open back with a slender or straight shaft. To strengthen the turbine wheel, Melett has developed a full back shaft and wheel solution that reduces the risk of fatigue on the inducer diameter.
Why two different types? Early turbochargers incorporated a slender shaft in their design. This shaft was perceived to be lighter and provide less resistance, increasing performance. However, with advancements in turbocharger technology, a straight shaft was developed which provides extra strength and rigidity, and in theory makes the turbocharger easier to balance.
Compressor Wheel Variations
As turbochargers develop, operating conditions have altered significantly. Turbochargers are spinning faster than ever before and subjected to higher temperatures.
As a result, this has led to significant development in compressor wheel design to cope with ever changing conditions.
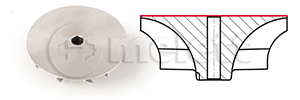
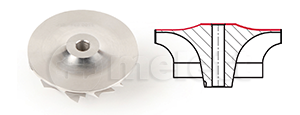
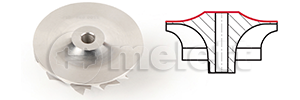
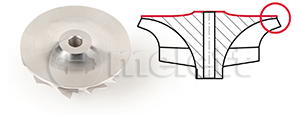
RHF4 Air Cooled & Water Cooled Bearing Housings
The RHF4 bearing housings are available in two variations; Air Cooled & Water Cooled.
Air Cooled: Ambient air and oil act as a cooling mechanism.
Water Cooled: High temperature applications need extra cooling to perform efficiently.
K03-4 Twin Feed & Single Feed Bearing Housings
Borg Warner – K03-04 / BV43/50 Bearing Housings
Please note: Before repair please ensure you have the right journal bearing for the bearing housing – failure will occur if they are mixed.
CHRA Explosions
GT12 Z-Bearings
Whilst it is seen to be a relatively new design, the Z-bearings design has actually been around since some of the very first mass produced turbochargers.
Cummins ST50 and Schwitzer 3LD both used the side of the journal bearing and the shaft and wheel hub as a thrust face. Garrett’s ‘Z-bearing’ first arrived with the Smart Car GT12 and the Ford GT1544Z turbo back in the late 90’s / early 2000 models. However, the current Z-bearing designs which are arriving in today’s aftermarket are very different from the older 3LD design.
The design of the Z-bearing is popular on the smaller turbos because it simplifies the assembly by incorporating the thrust bearing faces onto the ends of the journal bearing. The design means that there are fewer parts, and hence less room for accumulated tolerance and balancing errors. The detail of the oil ramping on the thrust face also includes some complex geometry rather than the standard linear ramping found on standard thrust bearings.
There are many different designs in the various GT##Z turbos. For the design process, Melett has carried out a full analysis of all the variations of the bearing and thrust designs in the latest aftermarket arrivals, including thrust diameters and material. After this analysis, we have simplified the number of variations down to four different styles, as follows:
1102-012-100 – Replaces the original GT12 Z-Bearing used on the Smart Car and Ford GT1544Z turbos and is identified with a single ring on the OD. The full repair kit is 1102-012-755;
1102-012-102 – Geometrically the same as the 1102-012-100, but is now produced using an improved high strength material specification and is identified with two rings around the OD. (OD 11mm);
1102-012-103 – Larger OD than the original GT12 journal and is identified with two rings on the OD. High strength material (OD 12mm);
1102-014-100 – For larger GT14 turbos – The OD and ID are the same as the 1102-012-103, however this bearing is identified by a much larger surface area on the OD and one groove in the narrow slot on the OD. High strength material;
Important Installation Information:
Orientation – As the bearings incorporate thrust ramping on their end faces, it makes them directional. This means that the bearings MUST be installed in the correct orientation or the ramping will be reversed, which will result in very early failure of the bearing system. All of the bearings have an identification groove to one side. The bearing should always be assembled with the groove to the Compressor side.
Retaining Screw – It is important that the journal bearing doesn’t rotate or vibrate during operation. The action of the oil load on the thrust face ramping increases the bearings rotational loads. This radial load is resisted by the anti-rotation pin, as such, the fit of the anti-rotation pin into the journal bearing hole is held to very tight tolerances. Any ‘play’ in the fit would quickly lead to wear and result in subsequent failure of the turbo.
To ensure a quality repair, it is advised that this anti-rotation pin is always replaced when reconditioning the turbo. Melett repair kits include the retaining pin as standard. Please ensure that all your build procedures for these new turbo designs are updated and all build staff are properly trained. Avoiding warranties doesn’t just help your business profitability, it also helps customers build confidence in the entire repair industry.
BV40 Machined from Solid 'MFS' Compressor Wheels
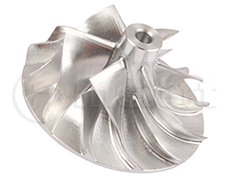
Melett BV40 Machined from Solid (MFS) compressor wheels replace the original BV40 compressor wheels and feature the new extended tip design.
Machined from solid compressor wheels are becoming increasingly popular as these new developments from the OE’s continue to arrive in the aftermarket. The wheels are fully machined and balanced on leading 5-axis machining equipment, and precision balanced on fully automated balancing stations with auto-correction.
Melett Part No. 1303-040-400